Common Rail Fuel Injector Denso 095000-6353 095000-6351 0 23670-E0050 for Hino Kobelco Sk200-8 Sk230srlc Sk260LC-8 Excavator Engine J05E
products detail
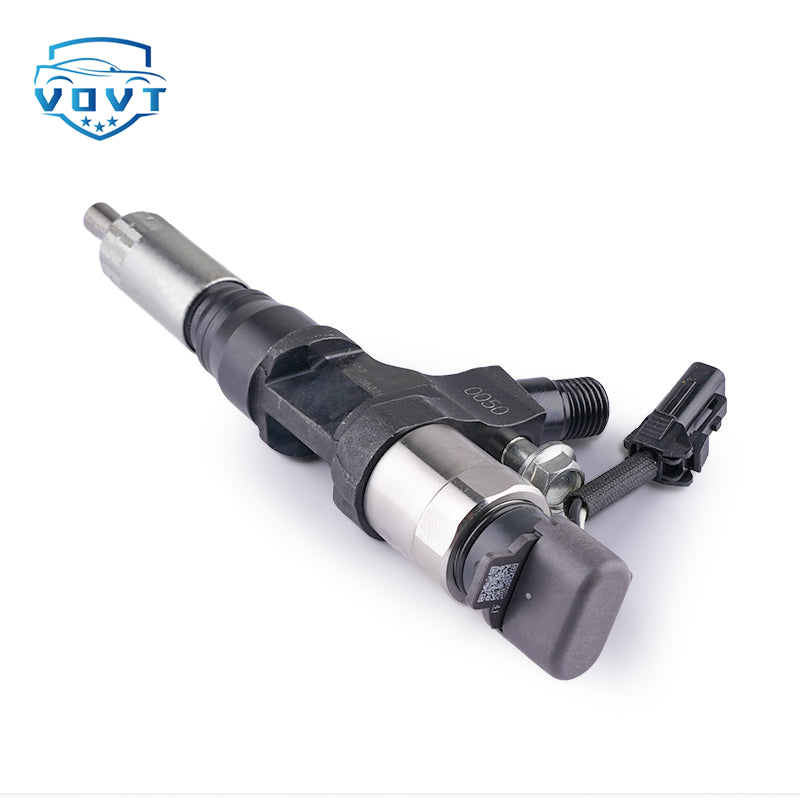
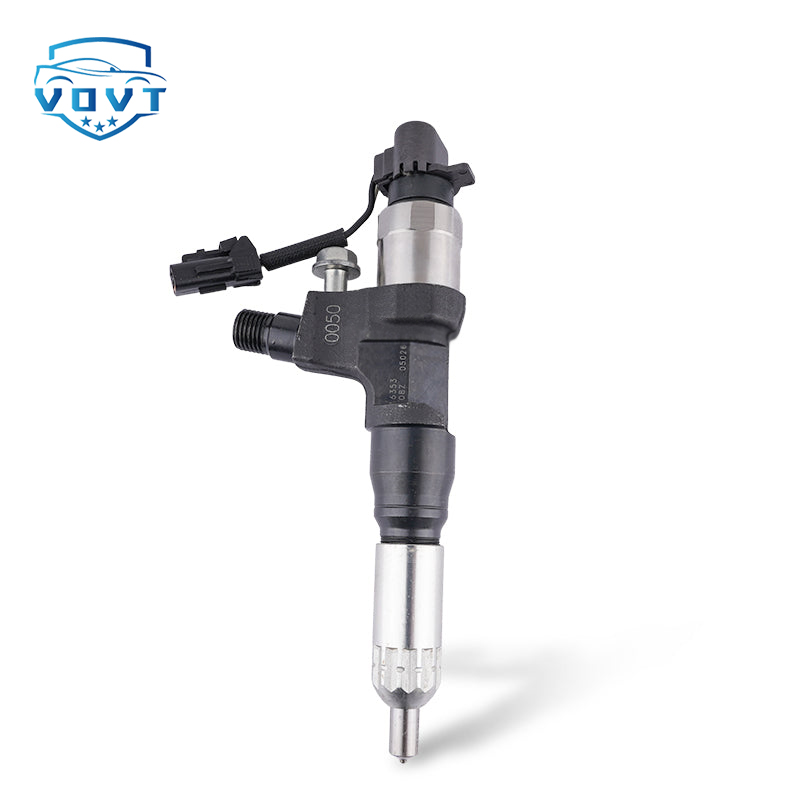
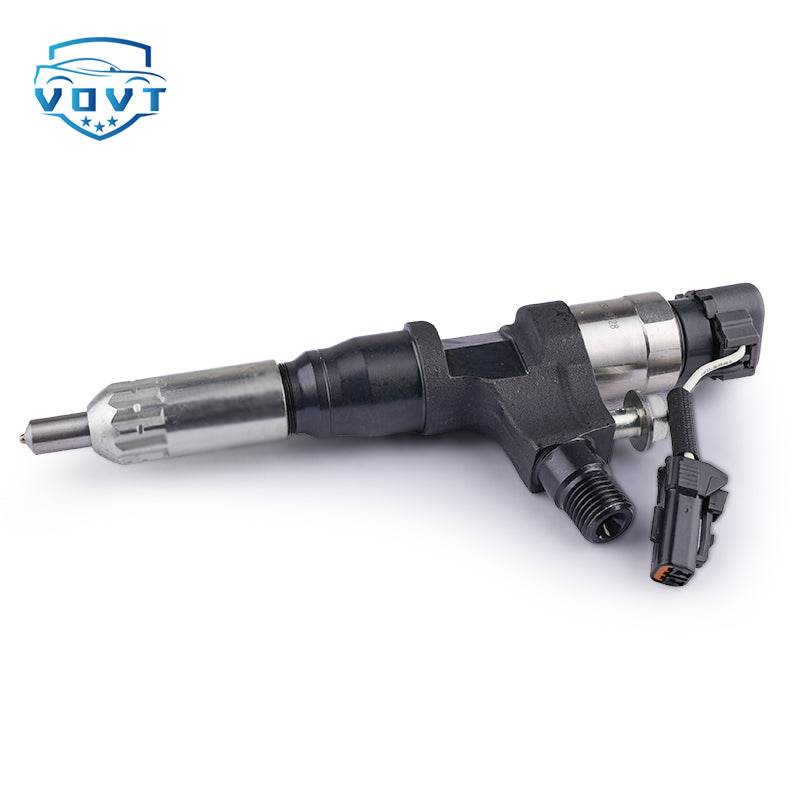
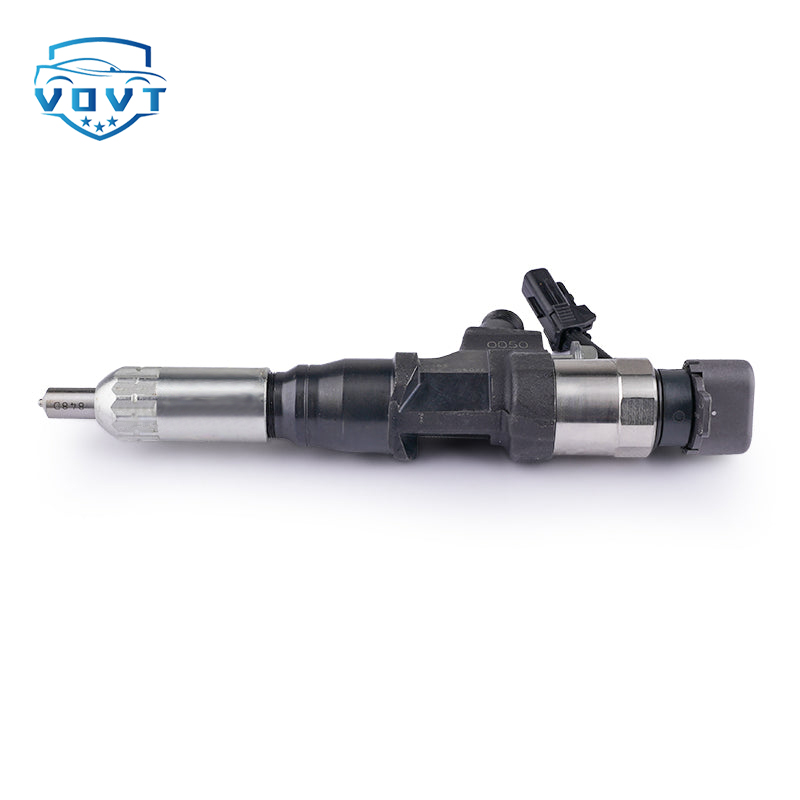
Used in Vehicles / Engines
Product Code | 095000-6350 / 095000-6351095000-6352 / 095000-6353/23670-E0050/VH23670-E0050A/VH23670-E0050 |
Engine Model | Hino Engine J05E |
Application | Hino Kobelco Excavator SK200,Hino Kobelco SK230SRLC,Hino Kobelco SK260LC-8 |
MOQ | 6 pcs / Negotiated |
Packaging | White Box Packaging or Customer's Requirement |
Warranty | 6 months |
Lead time | 7-15 working days after confirm order |
Payment | T/T, PAYPAL, as your preference |
There are a large number of joints in the grinding machine. According to the motion properties, the joints can be divided into fixed joints, movable joints and semi-fixed joints. The fixed joint mainly plays the role of fixed connection and support, including bolt bonding, taper fit, point welding, riveting, press fit, etc. The movable joint is the joint of two interrelated parts in the working state, such as guide rail joint, shaft and bearing joint, etc. The three rows of roller bearing joint in this paper is a typical rolling joint; The semi-fixed joint is sometimes fixed and sometimes relative movement of the joint, including friction clutch, clearance wheel, such as the electromagnetic clutch in this paper.
In the concave end face grinder for diesel engine oil nozzle studied in this paper, three rows of roller bearings play a key role in connecting rotary table and bed, and play a decisive role in the dynamic characteristics of the grinder. The linear contact between rollers and raceway is a difficulty in dynamic modeling. Early modeling of rolling bearing dynamics mainly focused on the hypothesis between rolling body and raceway. Harris, Jones and PalmgrenBrandlein studied the nonlinear relationship between the visibility and load of cylindrical roller bearings. Based on the rigidity of raceway of cylindrical rolling bearings, Gargiulo studied the stiffness variation with load. Y.sejin et al. cut the surface of the rolling body and the surface of the track into small pieces and calculated the stress distribution separately instead of the original stiffness matrix calculation method. The disadvantage is that the influence relationship between each piece is not considered, resulting in a large error.