New Common Rail Dlla152pm1003 M1003p152 Injector Nozzle for Fuel Injector A2c59511611 5ws40250 7t1q-9f593-Ab for Ford Focus Mk II 1.8t 2004-2008
products detail
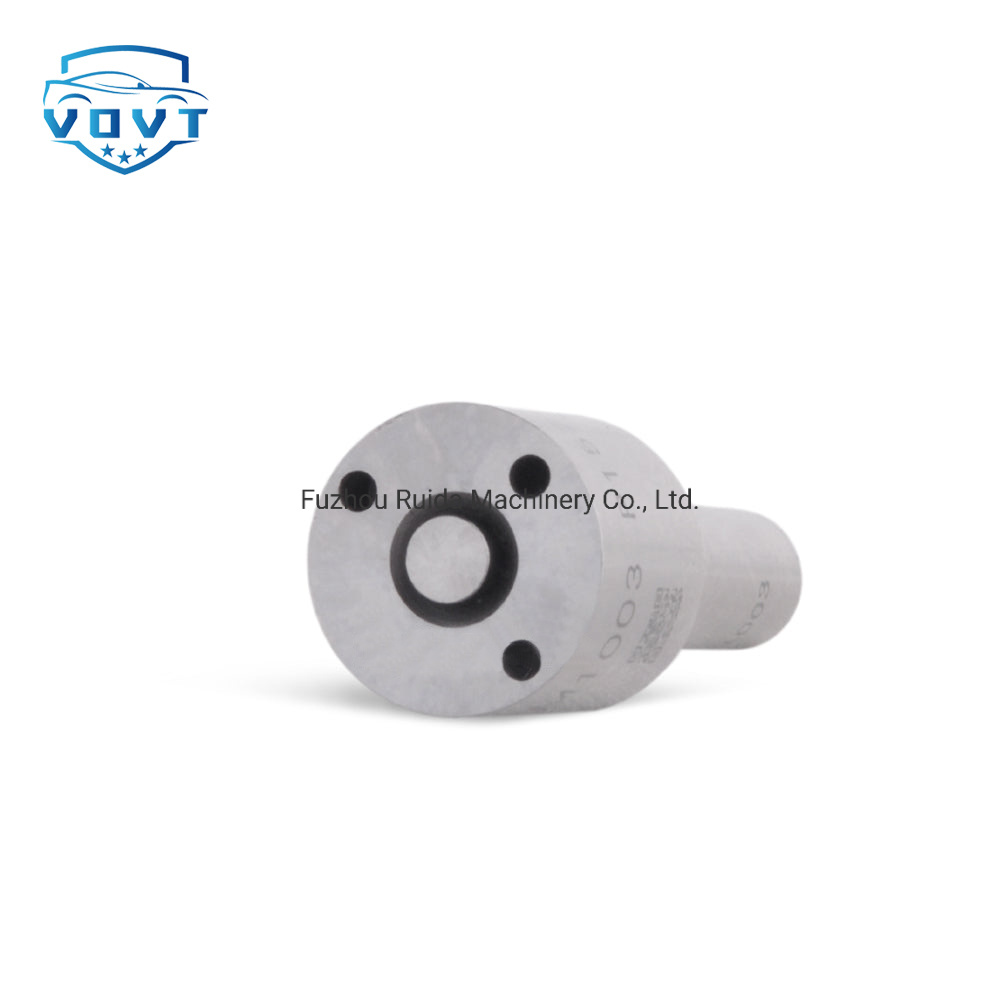
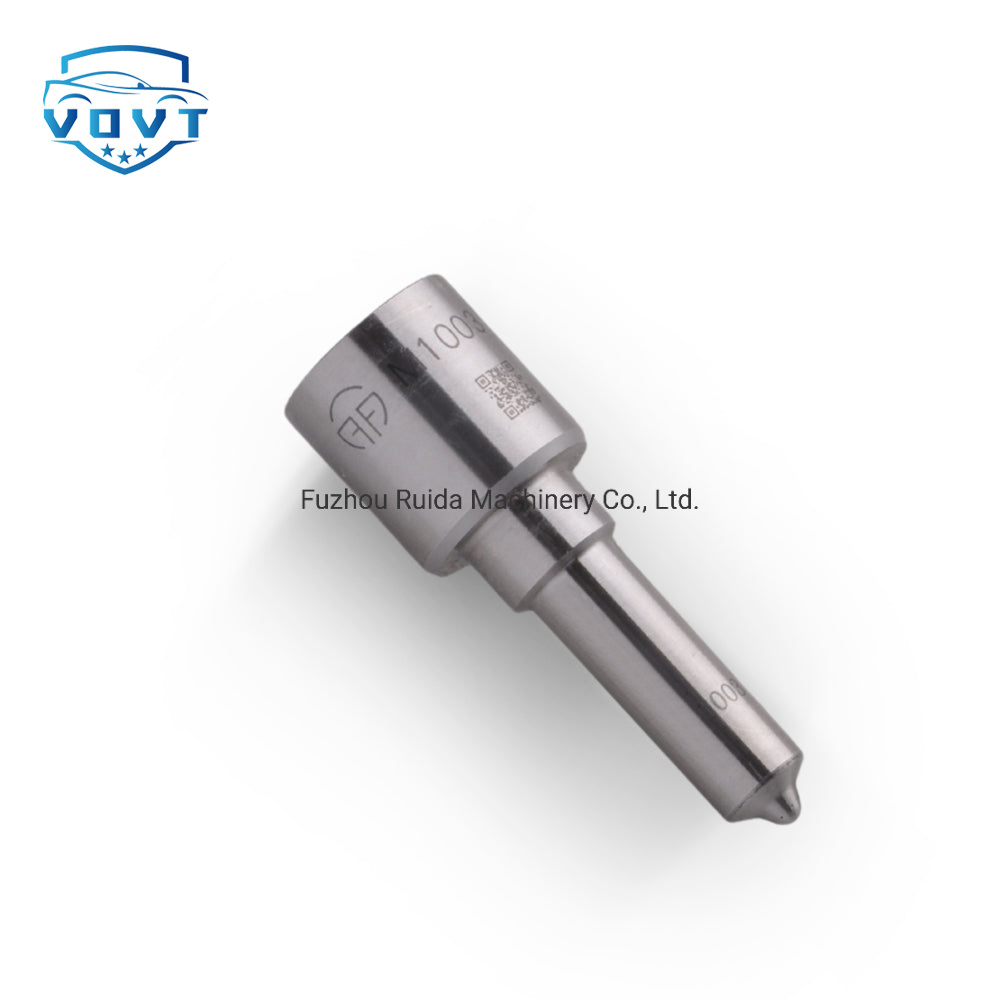
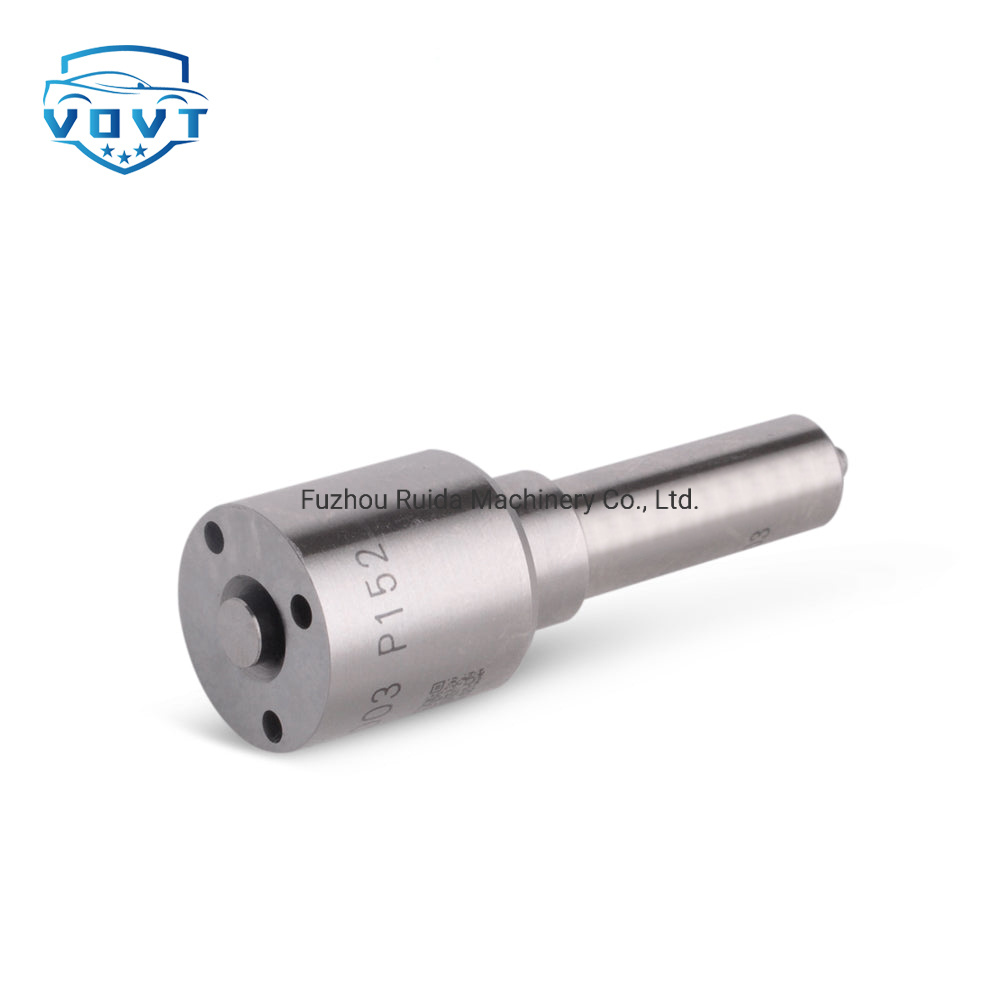
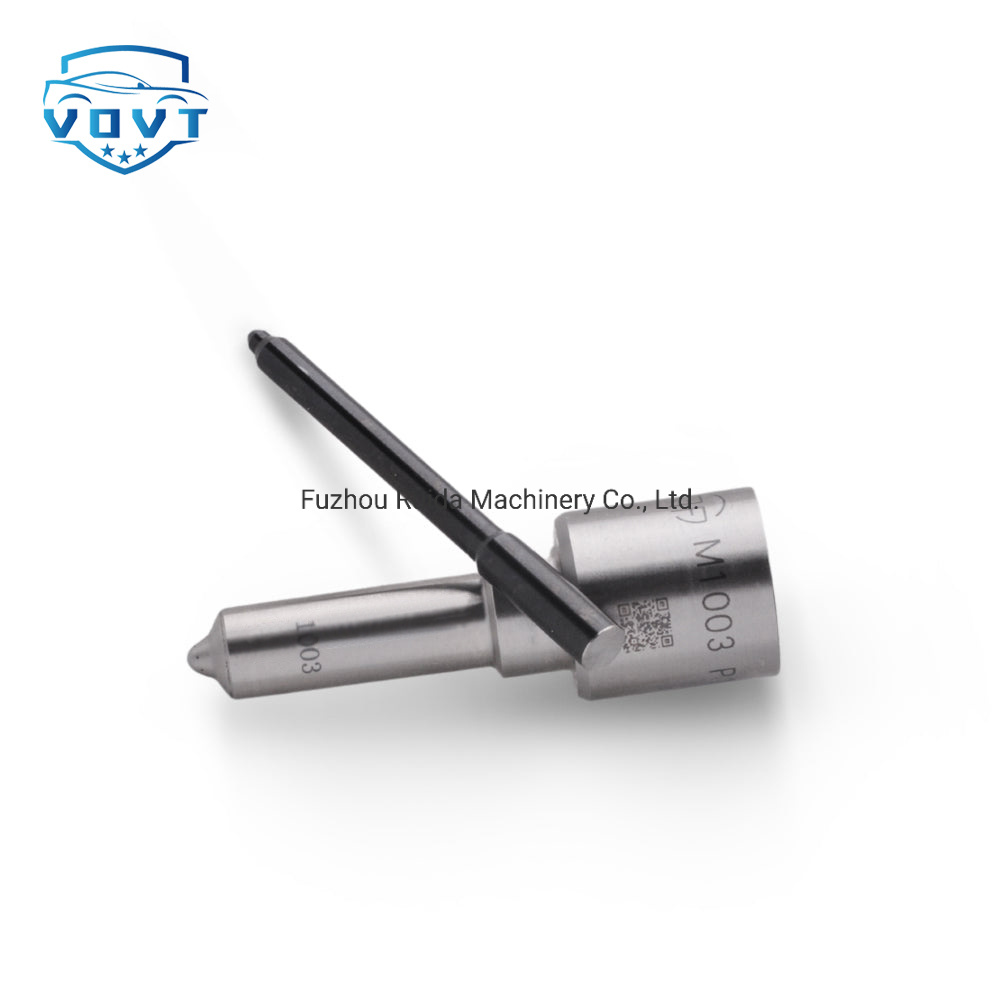
Used in Vehicles / Engines
Product Code | M1003p152 |
Engine Model | / |
Application | / |
MOQ | 6 pcs / Negotiated |
Packaging | White Box Packaging or Customer's Requirement |
Warranty | 6 months |
Lead time | 7-15 working days after confirm order |
Payment | T/T, PAYPAL, as your preference |
Delivery Method | DHL, TNT, UPS, FedEx, EMS or Requested |
Hydraulic extrusion grinding
Hydraulic extrusion grinding is to make semi-solid abrasive extruded through some parts (such as pressure chamber and jet hole), deburring, polishing and chamfering of channel surface and corner, as shown in Figure 1. The machine can control the extrusion pressure, abrasive flow and velocity. Different kinds of grinding, particle size, density and carrier viscosity can be used to produce different extrusion grinding effects. The carrier is generally a kind of flexible semi-solid polymer, adding a certain amount of abrasive mix. High viscosity near-solid carriers are used to evenly grind the inner walls and large channels of parts. Lower viscosity is generally used for corner chamfering and small channel grinding. When the abrasive is squeezed into the restricted channel, the viscosity of the abrasive increases, holding the scrub firmly in place. At this viscosity, the abrasive will grind the passage through. The abrasive mass thickened by extrusion is discharged through a restricted channel, that is, the normal viscosity is restored, resulting in little or no grinding. Abrasive viscosity, extrusion pressure and the size of the channel determine the flow rate of abrasive, affecting the grinding amount, grinding uniformity, the size of corner chamfering. Slow flow rate is suitable for uniform grinding, high flow rate will produce large corner roundness. Extrusion pressure range is 0.7 ~ 22MPa, abrasive flow rate is more than 3801/min. The most commonly used scrub is silicon carbide, but cubic boron nitride, alumina and emery are also available. The size of sand particles ranges from 0. 005 to 1.5mm. Fine sand can achieve a high finish. The depth of cutting caused by sand on the workpiece depends on the selected extrusion pressure, abrasive viscosity and sand size.