New Common Rail Injector Nozzle M0011p162 Pdlla162pm0011 for 5ws40539 03L1302778 A2c59513554 Injector Compatible Wtih VW Seat Skoda Audi 1.6
products detail
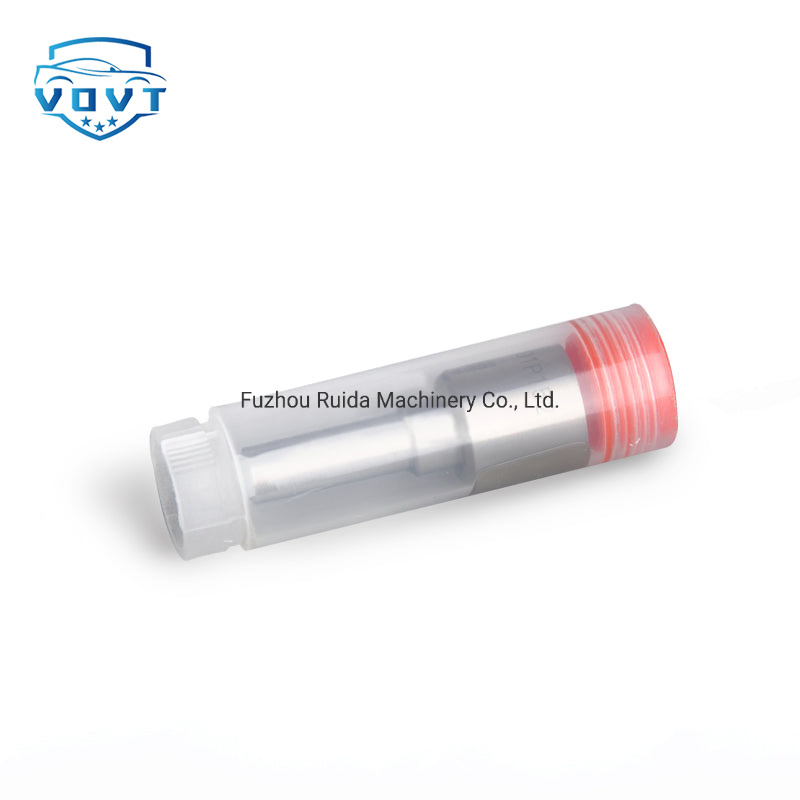
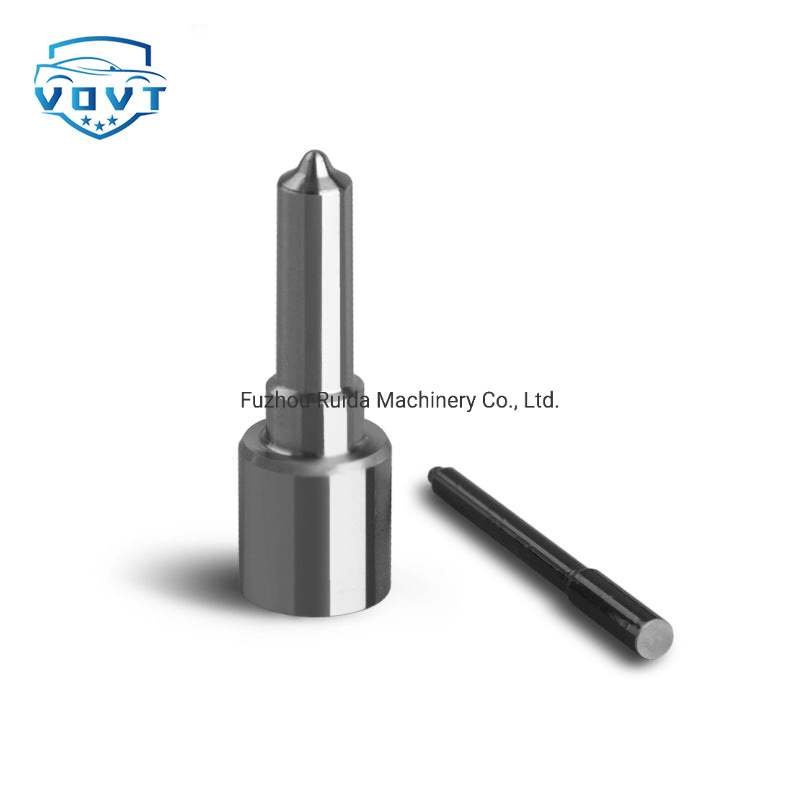
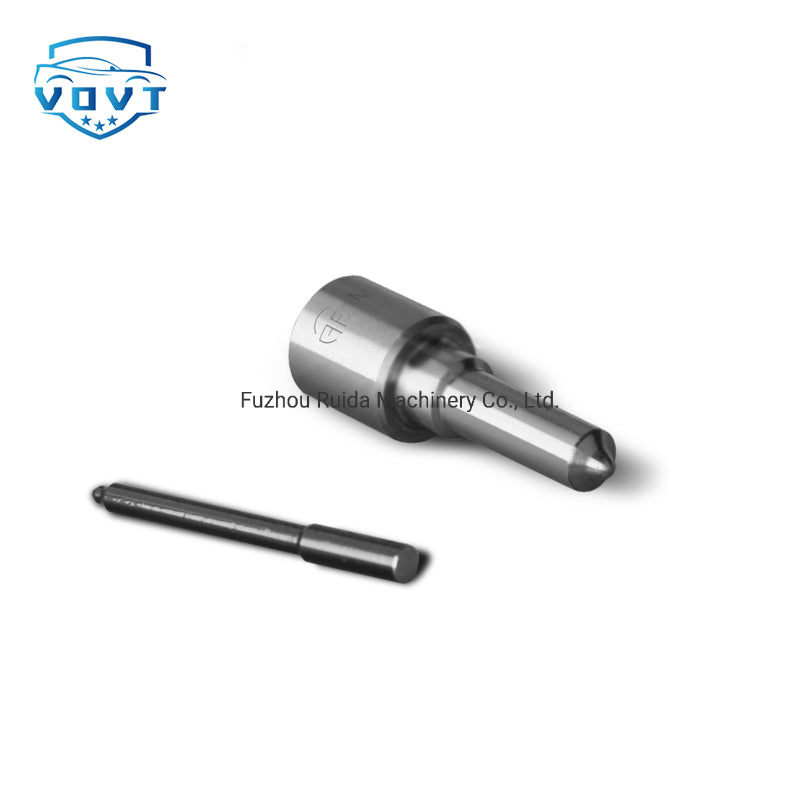
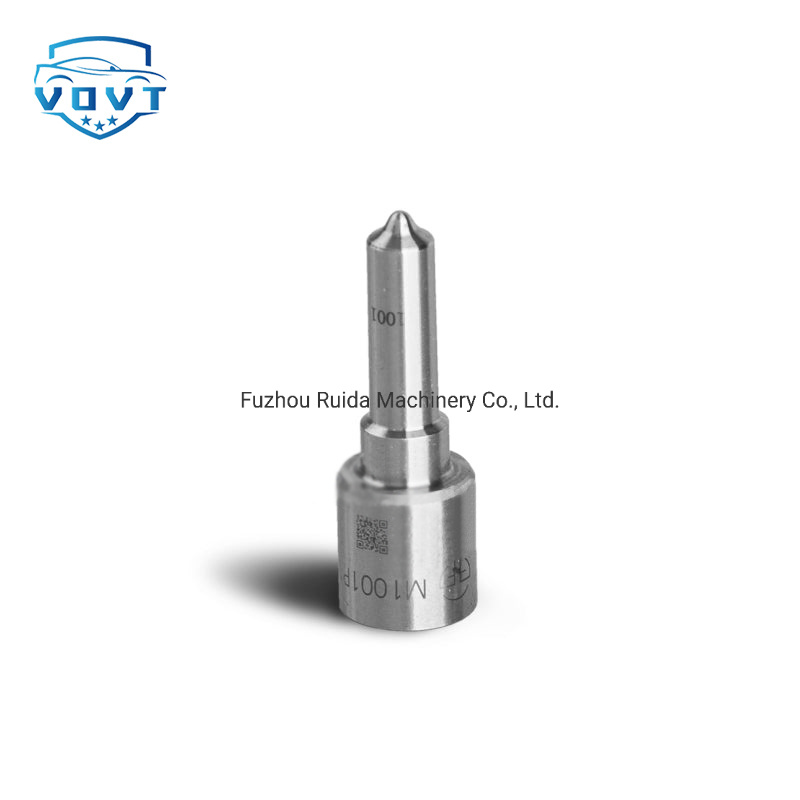
Used in Vehicles / Engines
Product Code | A2c59513554 |
Engine Model | / |
Application | / |
MOQ | 6 pcs / Negotiated |
Packaging | White Box Packaging or Customer's Requirement |
Warranty | 6 months |
Lead time | 7-15 working days after confirm order |
Payment | T/T, PAYPAL, as your preference |
Delivery Method | DHL, TNT, UPS, FedEx, EMS or Requested |
FAQ
- The technology center of Ruida Company has carried out the hydraulic extrusion grinding process test on the 4-hole J series nozzle (aperture is 0.30mm) produced by the company. The average flow rate of 20 pairs of nozzle body was increased by 27.7% after grinding. The comparative test results show that the specific fuel consumption of v engine decreases by 4~10g /kW - after the nozzle is LR6105Q diesel engine and the orifice is rounded h, smoke decreases 0.5 ~ 1.0Bosch unit, exhaust temperature decreases about 20℃, if the oil supply of the oil pump is not changed, the calibrated power of the diesel engine can be increased by 10~ ~ 15%.
Thin liquid flow grinding
Compared with the extrusion grinding method, v this is a kind of lower viscosity, almost to the ink state of a medium, with a certain flow rate through the jet hole, to achieve the purpose of grinding holes, deburring and hole chamfering. This is a device developed by DYNETICS. The medium of this processing method is a low viscosity naphthenic mineral oil, and a certain amount of additives to change the flow, and then add 400 to 1200 particle size of emery. The medium must have sufficient viscosity to maintain a uniform and consistent distribution of abrasive particles at low shear rates. At high shear rates, when entering the orifice, the viscosity must be reduced to allow it to flow through the orifice at high speeds, similar to the flow of diesel oil. The pressure range in the process is 0.35 ~? OMpa: 2.8MPa is commonly used. Medium temperature 25 0.2℃. Because of the low viscosity and low wear of the medium, the flow meter can be directly used in the medium channel to accurately detect the flow rate of the workpiece in real time, so it is easier to achieve strict flow control than the extrusion grinding process.